Established CO2 reduction technology using hydrogen in blast furnaces ~ Achieved a CO2 reduction of 43% at the world's first test furnace, ahead of development goals ~
2024/12/20
Nippon Steel Corporation
Nippon Steel Corporation (hereinafter referred to as Nippon Steel) is working on the development of three ultra-innovative technologies under the "Nippon Steel Carbon Neutral Vision 2050," with national support. One of these, "Hydrogen Reduction in Blast Furnaces," is a technology that significantly reduces CO2 emissions by using hydrogen instead of Coal for the reduction of iron ore in blast furnaces. Recently, a world-first CO2 reduction of over 40% (actual value 43%) was achieved in the test furnace, ahead of the development goals.
Currently, there are approximately 800 blast furnaces worldwide (including 20 in Japan), primarily in East Asia, with the world's blast furnace manufacturers competing fiercely in the development of decarbonization technologies, including China, which accounts for about half of the world’s crude steel production. The CO2 reduction achievement of 43% in this test furnace significantly exceeds the disclosed performance values both domestically and internationally, indicating that Nippon Steel is a global leader in the development of decarbonization technologies.
Nippon Steel has been conducting tests of the CO2 reduction technology using heated hydrogen (Super COURSE50 technology) in the hydrogen reduction test furnace (volume 12m3) at the Kimitsu area of the East Japan Works since May 2022. To date, significant progress has been made, confirming a CO2 reduction of 22% in 2022 and 33% in 2023, which represent the highest standards in the world. In tests conducted from November to December 2024, a CO2 reduction of 43% was confirmed, exceeding the world standard.
In the current blast furnace process, iron ore, which is iron oxide, is reduced and melted using Coal (carbon), but while reduction by Coal (carbon) is an exothermic reaction, reduction by hydrogen is an endothermic reaction. This creates technical challenges, making it difficult for the reduction reaction to progress and for the iron ore to melt. In this trial, by increasing the use of hydrogen instead of carbon and improving the thermal balance within the blast furnace during the use of heated hydrogen, a CO2 reduction of 43% was achieved.
Based on the establishment of hydrogen reduction technology in the test furnace, Nippon Steel will continue to advance the development of technologies that reduce CO2 emissions from the steelmaking process by more than 50%, and accelerate efforts toward practical application in large blast furnaces.
(*) In January 2022, it was adopted by NEDO (National Research and Development Agency for New Energy and Industrial Technology) for the Green Innovation Fund, and in November 2023, the fund was expanded. This development is being advanced under the consortium of four companies: Nippon Steel Corporation, JFE Steel Corporation, Kobe Steel, Ltd., and the General Incorporated Foundation for Metal-based Materials Research and Development Center.
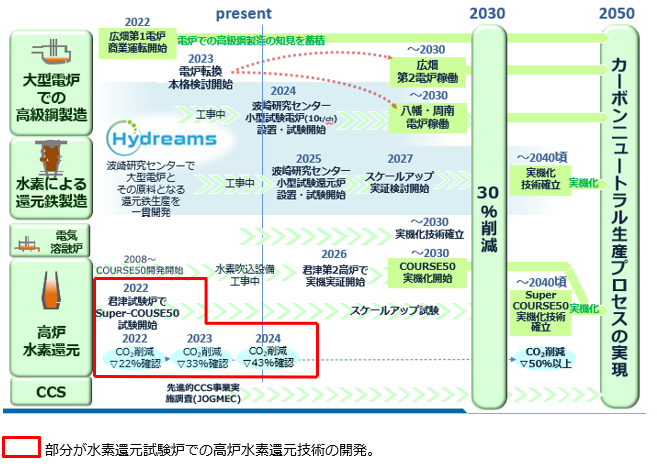
Return to the list of press releases.